PMR-T1A
Intelligent operation and maintenance system for belt conveyors
The system is composed of PMR-T1A belt conveyor rail inspection robot and PMR-A1A belt tear detection system. Through inspecting the coal conveying process, the risks existing in the conveying process are found in time. The system adopts precision, modular and standardized design to meet the inspection requirements in various environments.
The collected information is analyzed by advanced AI intelligent image processing algorithm. The purpose of fault diagnosis and risk identification is achieved through deep learning and other methods.
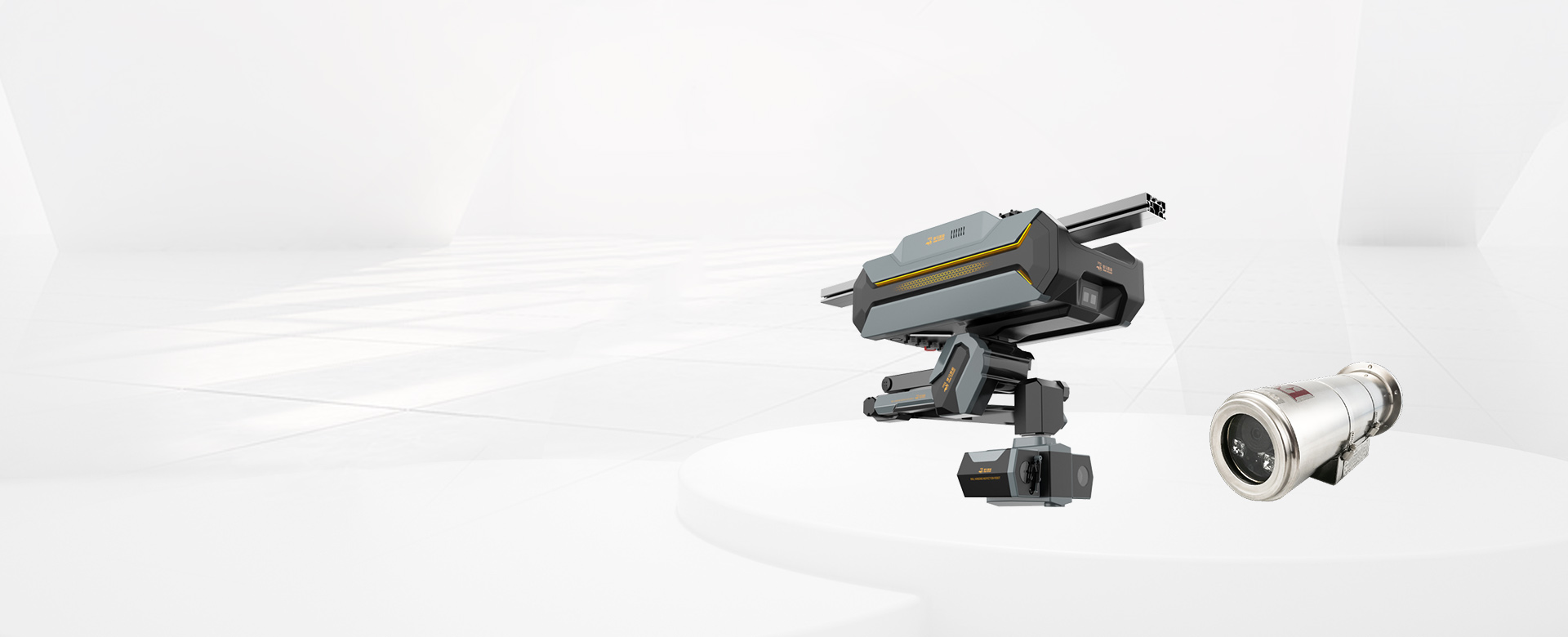
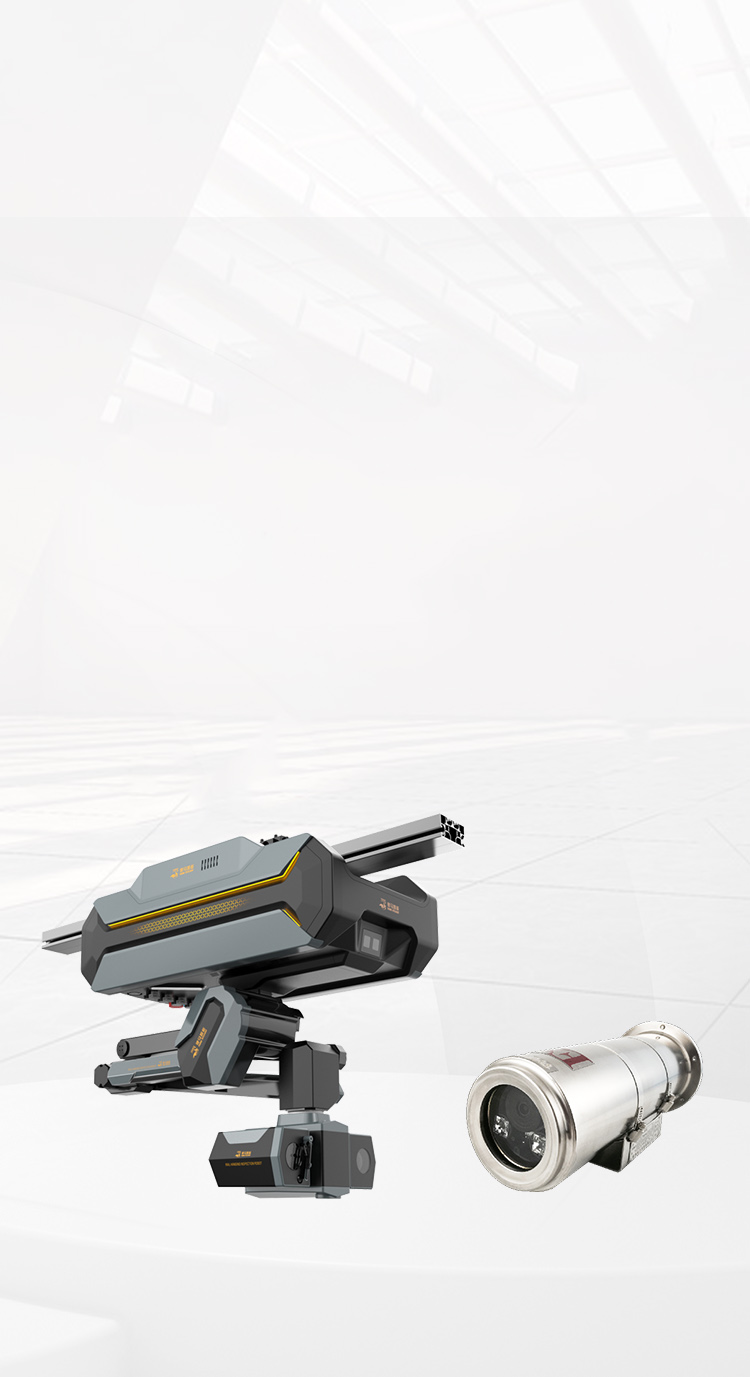
Functional characteristics
-
Automatic identification and temperature measurement of rollers Alarms
Dynamic identification of rollers and local infrared temperature measurement, find abnormal heating and alarm in time
-
Belt tear
Fast monitoring of belt tear, timely alarm
-
Belt deviation
Real-time monitoring of belt deviation, timely alarm
-
Coal leakage monitoring
Monitor the coal leakage in the coal transport tunnel in real time, take corresponding measures timely, and notify the operation and maintenance personnel
-
Foreign object monitoring
When a foreign object is detected in the collected image, the alarm system is triggered
-
Fire monitoring
Locate the fire position quickly and generate an alarm
-
Environmental monitoring
Real-time monitoring of toxic and harmful gases such as CH4, CO, CO2, H2S, O2, as well as abnormal temperature, humidity, and smoke, and timely alarm
-
Area intrusion monitoring
Define hazardous areas and alarm immediately if any personnel are found to have crossed the boundary
-
Personnel behavior monitoring
Identification and warning of behaviors such as wearing safety helmets, smoking, falling to the ground, abnormal detention, and seeking help
Product advantages
-
Dynamic high-speed inspection
Through efficient video stream processing technology and data transmission technology, roller temperature measurement and belt tear monitoring can be completed during uninterrupted walking. The inspection frequency can reach 1H/time, so anomalies can be detected in a timely manner, effectively reducing the risk of loss.
-
Automatic identification and temperature measurement of rollers
Use AI algorithm to automatically identify the rollers and conduct infrared temperature measurement on the identified roller area. The image recognition speed is faster and the recognition accuracy can reach 99%.
-
High flexibility folding arm
Collect images of the bottom and hidden points of the belt conveyor without blind spots, timely discover the working conditions of the bottom and other hidden points of the belt conveyor, reduce blind spots in the field of view, and achieve full coverage of belt conveyor monitoring points.
-
Support offline running
After the network is disconnected, the robot can normally perform inspection tasks and charge autonomously without data loss. When the network is restored, the robot will retransmit data to the centralized control platform.
-
Support edge computing
The robot itself has AI computing ability, and the local computing efficiency is higher and the response is faster. It reduces the dependence on background AI servers and AI algorithm boxes, reduces network dependence, and achieves true autonomy to run autonomic computing.
-
Strong environmental adaptability
It can achieve 45° slope climbing, with a minimum turning radius of 500mm. It adopts a closed chamber structure design, with a protection level of up to IP67, ensuring stable operation in harsh environments such as dust and humidity on the coal transport trestle.
-
Long-term stable operation
Strictly tested and verified components and materials are used, multiple load, impact, speed, and swing tests are conducted before delivery, and program design is optimized, it can operate stably for more than 6 months without downtime, shutdown, or serious malfunctions.