PMR-W1C
Bio-Inspired Manipulation Robot
The live operation robot is equipped with an integrated robotic arm and an end that can automatically replace operating tools. It uses multi-principle technologies such as visual servo and is remotely controlled through a computer program to complete routine operation tasks and realize comprehensive and intelligent inspection of the operating status of various types of electrical equipment and the operating environment.
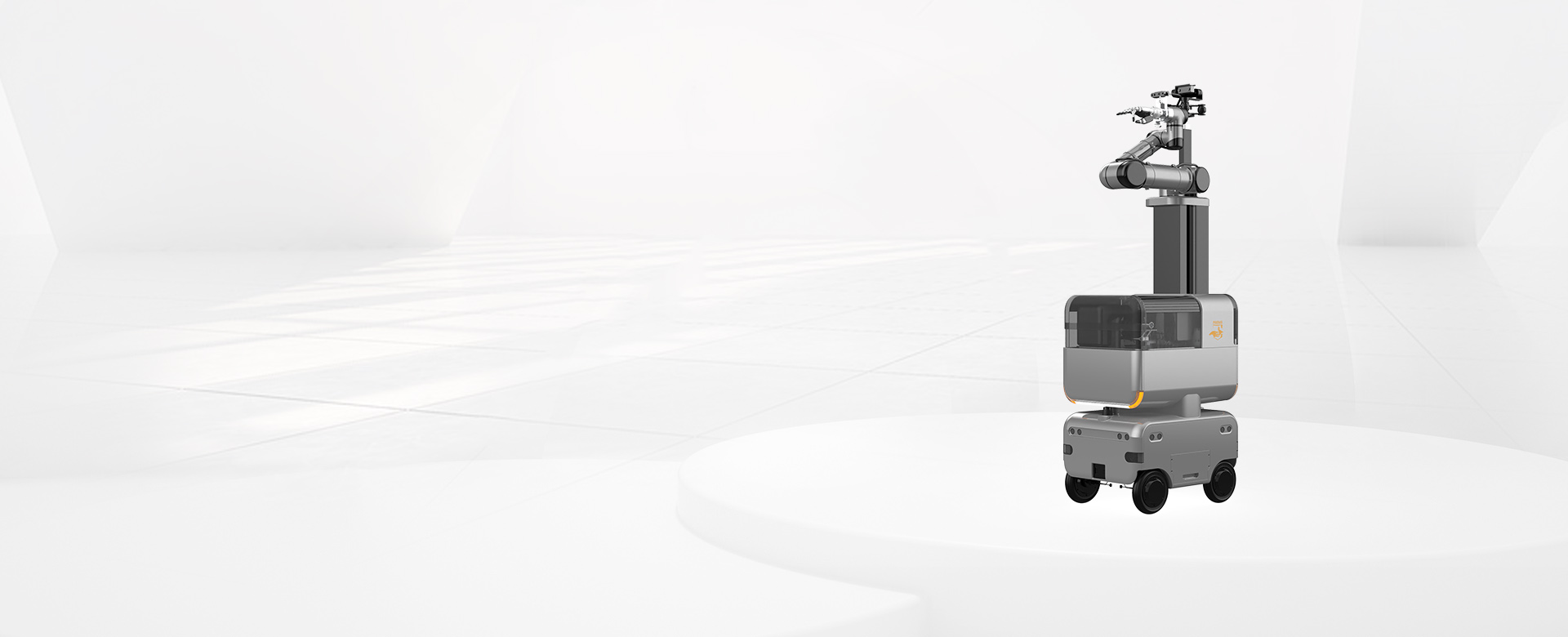
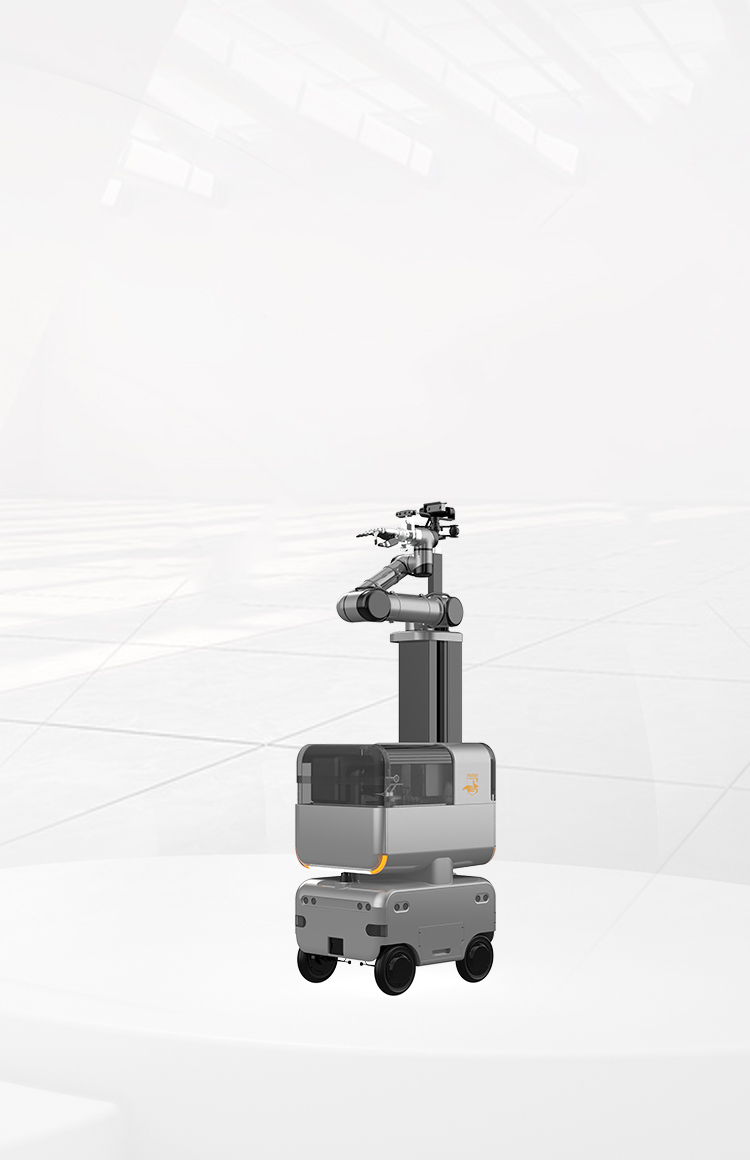
Functional characteristics
-
3D visual recognition
Autonomous positioning of operational targets改成Independent positioning of operation target
-
Flexible operation
Robotic arm with six degrees of freedom for switch operation tasks of large height spans
-
Multi-sensor fusion
The arm is equipped with systems such as partial discharge, image recognition, infrared thermal imaging, and partial discharge sensors to independently detect meters, temperatures, and equipment partial discharge quantities
-
Remote control
No on-site operation is required, and the robot can be controlled to complete switch opening and closing and equipment state switching through remote control system
-
VR system
Combined with the semi-autonomous control mode of man-machine cooperation, multi-principle technology such as visual servo, compliant control and force feedback is used to complete the routine operation task of the robot through computer program remote operation
-
Bionic system
Through the deep learning of the operating robot, the operation actions of the object to be operated can be automatically recorded
Product advantages
-
Single arm with dexterous hand
Single hand has 6 degrees of freedom and 12 motion joints, combined with force-position hybrid control algorithm, with sub-millimeter positioning accuracy and several kilograms of load capacity, can simulate the human hand to achieve precise grasping operations.
-
Millimeter level precision control
The 3D navigation technology is used to independently locate the operation target, the feedforward PID+ voltage and current double closed-loop control, and the modular power component + 6-axis attitude adjustment + mechanism design can complete the integration of a variety of complex operations. The vision closed-loop correction based on the depth camera + high-precision attitude adjustment system + machine learning algorithm can ensure the accurate positioning of the operation.
-
A variety of end-operation tools
The tool box supports multiple mechanical terminals, which can be automatically changed according to field requirements, so that the robot can operate flexibly in complex environments.
-
Long-term stable operation
Strictly tested and verified components and materials are used, multiple load, impact, speed, and swing tests are conducted before delivery, and program design is optimized, it can operate stably for more than 6 months without downtime, shutdown, or serious malfunctions.
- Previous:no more
- Next:Live operation robot (1st generation)
